The double ejection system is mainly used for molds after an ejection, the product still can not be successfully removed or forced out there will be damaged.
There are several common situations that require a double mold ejection system:
1. When the product has an under-cut to demold. The location of the red internal under-cut shown in figure a, due to space constraints, it is not convenient to do another demold system, so we consider force demold.
Force demold requires that there must be enough space on the back of the under-cut to allow rib deformation. the usual way is to make the under-cut part on the stripper bar. After the first stage of the ejection, the rib where the under-cut is located is completely out of the core, meanwhile, the ejector plate where the stripper bar is located stops moving, and the other ejector plate where the other ejector pin is located continues to eject, forcing the product to eject the stripper bar.
2. When gate and product have the sequence of action. For some products, sub-gate and product synchronization ejected, the gate may scratch the product, then we need to let the product before gate eject, stagger the position of the product and gate.
As shown in Part b in Figure 1, when the product is synchronized ejected with the gate, the sub-gate has the possibility to damage the product when it is elastic back after disconnecting the impression, and the product with the gate should be staggered ejected.
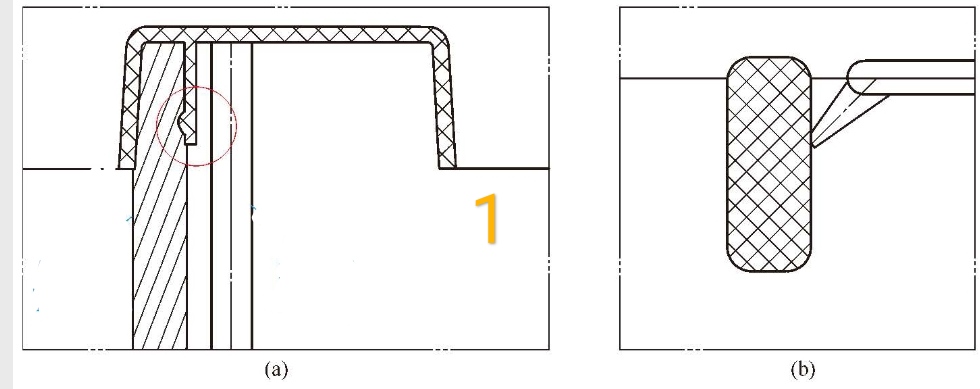
3. Fully automatic production of molds. After mold ejection, the product is still hanging on the ejector pin, can not fall down automatically, affecting fully automatic production, or the product holding the flat ejector pin, need to use a greater force or shake the product to remove the product.
4. When there is both an ejector pin and an empty ejection on the product, you need to let the ejector plate first eject the distance of the empty ejection, and then eject out with it.