In the design of mold structure, due to the need for structural action, it is often necessary to control the sequence of opening and close molds between the moldboards, different order control mechanisms, the order of implementation are different. The following is our common use of the open mold sequence control mechanism.
The open mode sequence control mechanism is shown in Figure 1,
the application example is shown in Figure 2.
Notice:
This control mechanism belongs to the mechanism that restricts one or two fast plates to be opened after the other plates have been opened.
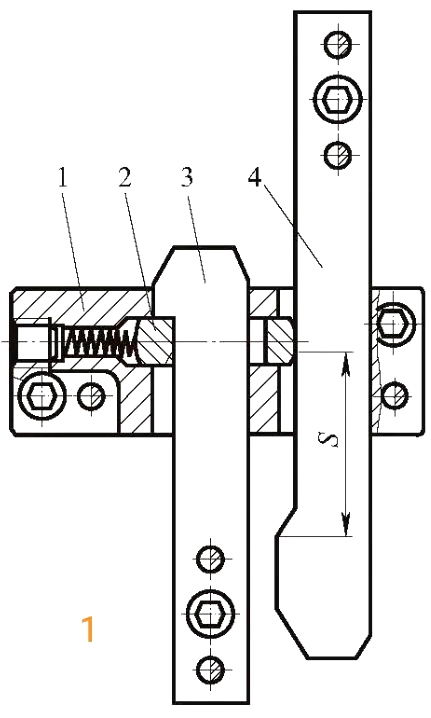
In figure 1:
Number 1 stands for fixing pedestal.
Number 2 stands for lever pin.
Number 3 stands for drawhook.
Number 4 stands for Pull block.
Capital letter S stands for mold opening stroke.
As shown in Figure 2, the mold requires that the A and B plates must be opened after the panel and the A board have been opened.
The principle of open mold action is shown in Figure 3, check the below pictures.
a. Under mold clamping state, the position of each part.
b. The status of the lever pin when the pull block is moved to the pre-dial.
c. Pull the block to move the lever pin, let out the drawhook to move the space.
d. The mold continues to open, the drawhook is removed from the lever pin, and the opening action is completed.
Our design specifications:
1. In order to ensure the stable operation of the mechanism, its direction of motion shall be parallel to the direction of the opening mold. Therefore, dial block, drawhook, fixing pedestal, in the mold must do a good job of positioning, generally do two positioning pins, so that its relative position is accurate. Slightly larger molds, dials, and drawhook are secured with more than two screws, the fixing pedestal is secured with 4 screws, and the small mold can be secured with 2 screws.
2. Due to mold processing errors and mold thickness tolerances, the mechanism must be assembled after the mold is finished, and then installed and leveled by the fitter master.
3. In order to prevent premature wear, the lever pin should use quenching material, other parts can use P20 material nitriding.
4. Due to processing errors, assembly, and commissioning errors, and other factors, drawhook, lever pin, dial blocks between the inevitable gap, and over time, the mold in the production process will wear out, the gap will gradually become longer. If the gap affects mold quality or mold safety, it must be used carefully, or other auxiliary bodies must be added to ensure mold safety.
5. After opening the mold, it is best not to leave the fixing pedestal and let it hold the lever pin. Therefore, the limit should be done between the two boards.
6. If the model has sequential requirements, it must be completed in conjunction with the partnership sequential control body.